Unlocking the Potential of a CNC Parts Factory: Innovation and Excellence in Metal Fabrication
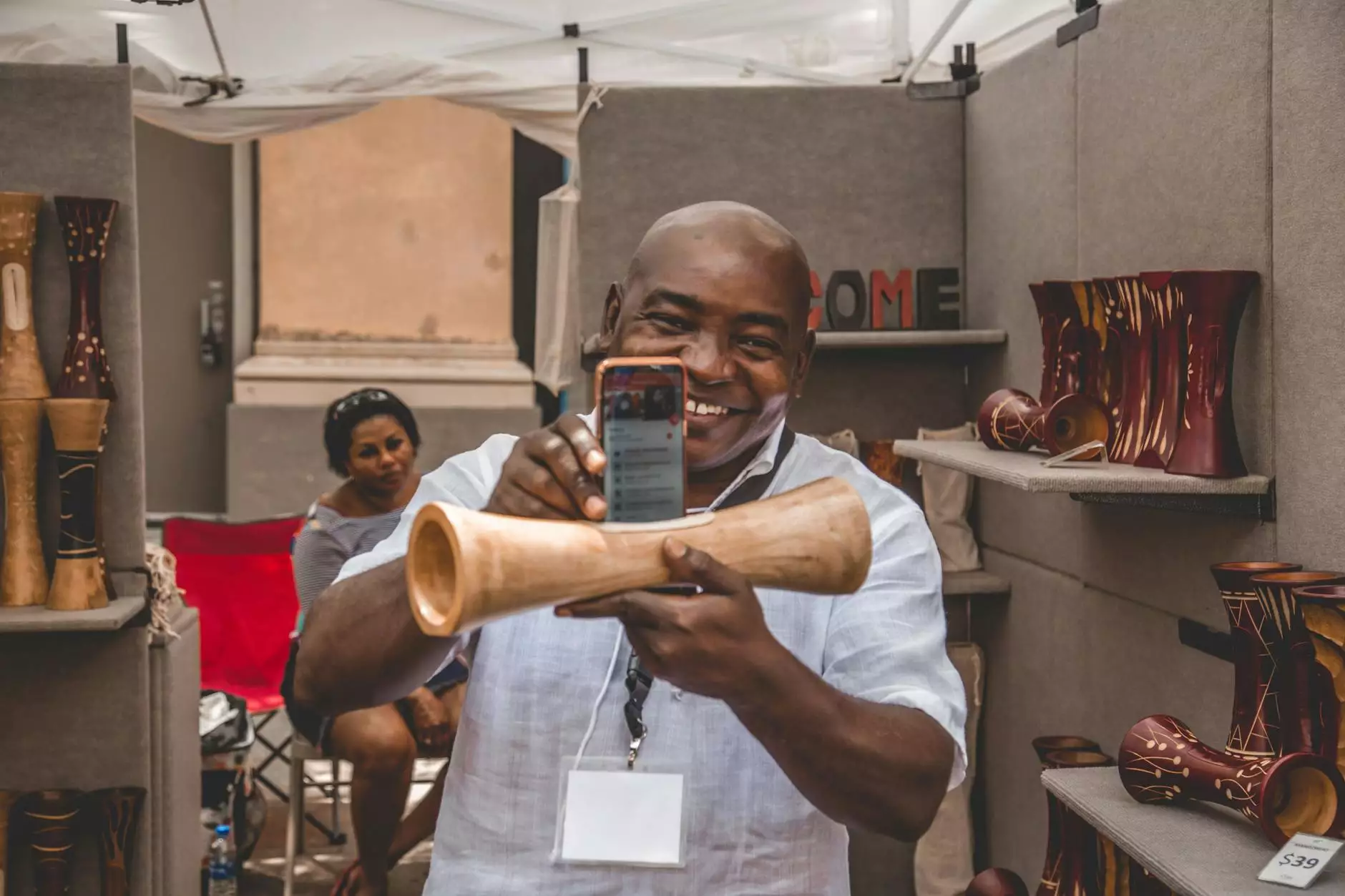
The modern manufacturing landscape is defined by precision, efficiency, and innovation. At the core of this new age of production is the CNC parts factory, a center of excellence that leverages cutting-edge technology to produce high-quality metal components. In this comprehensive article, we will delve into the significance of CNC (Computer Numerical Control) machining, how it transforms traditional manufacturing processes, and why businesses seeking metal fabricators should consider investing in CNC capabilities.
Understanding CNC Machining
CNC machining is a process that automates the movement of tools and machinery through computer programming. This advanced technique allows for heightened precision and the ability to produce complex parts with minimal manual intervention. Key features of CNC machining include:
- Automation: Reduces human error and increases output efficiency.
- Precision: Ensures consistent tolerance levels that meet industry standards.
- Flexibility: Easily adapts to different designs without the need for extensive retooling.
- Scalability: Accommodates both small and large production runs effectively.
The Growing Importance of CNC Parts Factories
The shift towards CNC parts factories is not merely a trend but a response to evolving market demands. Businesses in various sectors, from aerospace to automotive, require components that are not only reliable but also produced within tight timelines. A CNC parts factory addresses these needs by offering:
1. Enhanced Production Speed
CNC machines operate continuously with minimal downtime. This capability means that businesses can fulfill orders faster than ever before, supporting just-in-time (JIT) manufacturing practices.
2. Superior Quality Control
Each CNC machine is programmed to replicate designs with unwavering accuracy. This consistency leads to higher product quality and lower rates of defects, essential for maintaining customer trust.
3. Cost-Effectiveness
Although the initial investment in CNC machinery can be significant, the long-term savings through reduced labor costs, minimal material wastage, and increased production rates make it an economically sound decision for many businesses.
Applications of CNC Machining in Metal Fabrication
CNC machining plays a pivotal role in the field of metal fabrication across various applications:
Aerospace Industry
Aerospace components demand the highest levels of precision and reliability. CNC parts factories are essential to manufacturing critical parts such as:
- Aircraft frames
- Engine components
- Landing gear
Automotive Industry
The automotive sector has drastically benefited from CNC machining, which supports the production of:
- Engine blocks
- Transmission parts
- Custom bracket systems
Medical Devices
The production of medical devices requires stringent compliance with health regulations. CNC machining ensures that components are manufactured with both precision and consistency:
- Surgical instruments
- Implants
- Diagnostic equipment
Factors to Consider When Choosing a CNC Parts Factory
When seeking a reliable CNC parts factory, businesses must consider several factors to ensure they partner with a reputable manufacturer:
1. Technological Capabilities
Review the types of CNC machines available. Advanced factories typically offer a range of machinery, including:
- CNC milling machines
- CNC lathes
- Waterjet cutters
2. Expertise and Experience
A factory's experience in specific industries can greatly influence the quality and reliability of its output. Look for manufacturers with proven expertise in your sector.
3. Quality Assurance Processes
Investigate the quality control measures in place. Robust inspection protocols are crucial to ensure that every part produced meets the required specifications.
4. Turnaround Times
Consider the factory’s lead times for production. A partner capable of quick turnaround times can provide a significant advantage in fast-paced markets.
The Future of CNC Parts Factories
The landscape of manufacturing is continuously evolving, and CNC parts factories are at the forefront of this change. As technology advances, we can expect to see the following trends:
1. Innovations in Automation
With the advent of artificial intelligence (AI) and machine learning, CNC machines are becoming increasingly intelligent, capable of making real-time adjustments to optimize production processes.
2. Increased Customization
As consumer demand for personalized products grows, CNC parts factories are expected to enhance their capabilities to produce customized components more efficiently.
3. Sustainability Practices
Adopting eco-friendly practices will become more critical, with CNC factories focusing on reducing waste and utilizing sustainable materials.
Conclusion: Partnering with a CNC Parts Factory for Success
In conclusion, the role of a CNC parts factory in today’s manufacturing world is indispensable. By providing speed, precision, and cost-effectiveness, these facilities are revolutionizing the way metal parts are produced. For businesses in search of reliable metal fabricators, investing in a partnership with a CNC parts factory can lead to significant advancements in product quality and overall operational efficiency.
As the industry continues to evolve, staying informed about the latest advancements and understanding the capabilities of CNC machining is vital for any business aiming to thrive in a competitive market. With the right knowledge and partnerships, the potential for growth and innovation is limitless.