Understanding Injection Plastic Molding: Revolutionizing Manufacturing
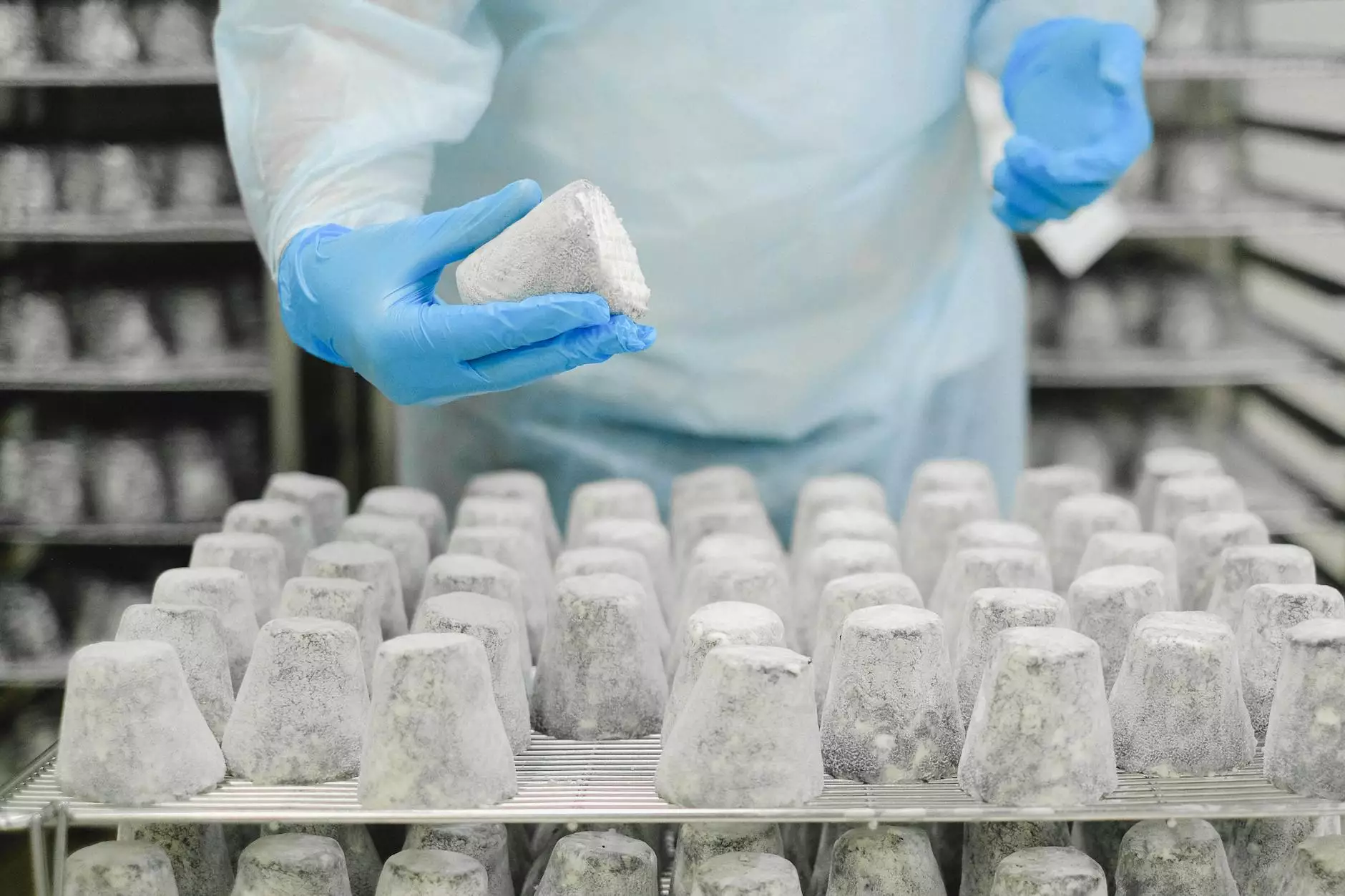
Injection plastic molding is a highly efficient manufacturing process that has transformed the way industries produce plastic components. As businesses increasingly seek to optimize production methods and improve product quality, understanding the intricacies of this technique becomes paramount. In this article, we delve deeply into the world of injection plastic molding, exploring its benefits, applications, and the critical role it plays in various sectors, including the work of metal fabricators at companies like deepmould.net.
What is Injection Plastic Molding?
At its core, injection plastic molding is a manufacturing process used for producing parts by injecting molten material into a mold. The process is particularly favored for its ability to create high volumes of parts with excellent precision, making it ideal for a variety of applications.
The typical injection molding process involves several key stages:
- Material Preparation: The first step involves the processing of raw plastic pellets, which are dried and prepped for injection.
- Injection: The prepared plastic is heated until it is molten and then injected at high pressure into a mold.
- Cooling: Once the mold is filled, the plastic cools and solidifies, taking the shape of the mold.
- Demolding: After cooling, the mold is opened, and the newly formed part is ejected.
- Finishing: The final step may include trimming, painting, or assembling the parts as needed.
Benefits of Injection Plastic Molding
Injection molding offers a wide range of benefits that make it the preferred choice for many manufacturers:
- Efficiency: The ability to produce large quantities of parts in a short time frame significantly reduces production lead times.
- Cost-Effectiveness: While the initial setup costs can be higher due to mold creation, the reduced per-unit cost at scale can lead to significant savings.
- Design Flexibility: Complex shapes and designs can be easily achieved, allowing for innovation in product development.
- Material Variety: A wide range of thermoplastics and thermosets can be used, providing options tailored to specific application needs.
- High Precision and Repeatability: Injection molding allows for tight tolerances, ensuring uniformity across large production runs.
Applications of Injection Plastic Molding
Injection plastic molding is utilized across numerous industries, showcasing its versatility. Here are some notable applications:
1. Consumer Products
From toys to kitchen utensils, injection molding is crucial in producing various everyday items. The ability to produce intricate designs at scale has made it a go-to for manufacturers.
2. Automotive Industry
Many parts, such as dashboards, lights, and panels, are fabricated using injection molding due to the strength and durability of the resulting components. This has contributed significantly to lighter vehicles and enhanced fuel efficiency.
3. Medical Devices
In the medical field, precision and reliability are critical. Injection molding is instrumental in producing components that meet stringent health regulations while maintaining high standards of quality.
4. Electronics
The production of housings, connectors, and various electronic components relies heavily on injection molding, thanks to its efficiency and precision.
The Role of Metal Fabricators in Injection Plastic Molding
While injection molding focuses on plastic, the role of metal fabricators is essential in creating molds that can withstand the pressures of the injection process. Companies like deepmould.net specialize in designing and manufacturing these molds, ensuring they meet the precise specifications required for various applications.
1. Mold Design and Engineering
Metal fabricators work closely with designers to create molds that allow for efficient production cycles. The mold design must account for factors such as cooling efficiency, ease of part ejection, and material characteristics.
2. Precision Machining
Fabricators use advanced machining techniques to produce molds that can achieve the tight tolerances necessary for high-quality production.
3. Material Selection
The choice of metal used for molds is crucial, as it must resist wear and withstand the high temperatures involved in the process. Common materials include steel and aluminum, each with its benefits.
Challenges in Injection Plastic Molding
Despite its many advantages, injection plastic molding is not without challenges. Understanding these can help businesses prepare and adapt accordingly:
1. Initial Costs
The creation of high-quality molds can be expensive, leading to significant upfront costs, especially for smaller businesses. However, these costs can be justified through mass production savings.
2. Design Restrictions
While the design flexibility is a benefit, there are also restrictions. For instance, parts must be designed to facilitate easy demolding, which can limit some creative design choices.
3. Material Limitations
Not all plastics are suitable for injection molding. Understanding the characteristics of different materials is essential to prevent defects during the manufacturing process.
Future Trends in Injection Plastic Molding
The future of injection plastic molding looks promising, particularly in the context of increasing automation and sustainability. Some trends to watch include:
1. Automation and Industry 4.0
Implementing robotics and advanced software in injection molding processes will enhance efficiency, reduce errors, and lower labor costs, paving the way for smart manufacturing.
2. Bio-based Materials
As sustainability becomes more critical for industries, the shift towards using bio-based and recyclable materials in injection molding is expected to rise, reflecting a broader commitment to environmental responsibility.
3. Advanced Simulation Technologies
Using simulation tools for mold design and production planning will enable manufacturers to predict potential issues and optimize processes before physical production begins, ultimately saving time and resources.
Conclusion: Embracing Innovation in Manufacturing
Injection plastic molding is more than just a manufacturing process; it is a gateway to innovation across multiple industries. As businesses like deepmould.net lead the charge in providing state-of-the-art molds, the potential for improved products and processes is limitless. Embracing this technology not only enhances operational efficiency but also paves the way for future advancements in manufacturing.
By understanding the benefits, applications, and emerging trends related to injection plastic molding, companies can position themselves at the forefront of their industries, driving productivity and profitability while delivering high-quality products to the market.